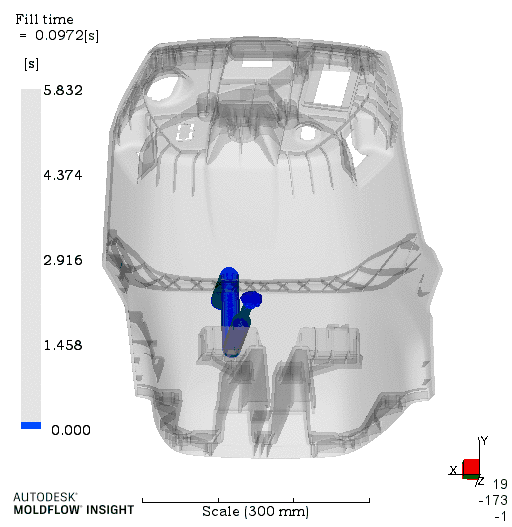
In this discussion, we will explore a part that was injection molded and scanned for deflection. Interestingly, the actual deflection did not match that of the analyzed part. Unfortunately, this can sometimes happen and when it does, it is the responsibility of the software expert to investigate why the predicted analysis results are not matching the floor results. This can be a challenging task.
In the engineering world, it is common to hear the phrase ‘garbage in equals garbage out’. In other words that phrase means that all inputs plugged into any set of calculations will directly influence the outcome of those calculations. When it comes to FEA, having correct input data is especially critical since technical software can only be as good as what is entered into each specific section. But what steps should be taken if you have ensured that the analysis is set up correctly yet, the analytical results do not match the results on the floor? In the sample study below, we will take a closer look.
For this study, we will look at a part that we will call the ‘console’:
We will compare the analytical inputs to the inputs used on the floor. Then, we will explore how the analytical results compare to those on the floor.
In preparation for any analysis, the user must take the necessary precautions to ensure that the inputs in the mold filling software are as accurate as possible.
Part model
1) Is the part model prepared so that it meets or exceeds the standards that the software supplier recommends?
Yes, the part was modeled as a 3D model and exceeds the recommended criteria.
Feed system design
2) Does the feed system match the final design of the finished product?
Yes, it was designed per the specifications provided by the tool shop.
Material data
3) Is the material data in the analysis the same as what is being used on the floor?
Yes
Is the material card comprehensive i.e., is it fully characterized?
Yes
Process inputs
4) Do the process inputs in the software match the floor inputs?
Yes, see the Table 1. Below
Once the inputs have been confirmed as optimal and correct, we inspect the results and compare them.
First, we examine the filling pattern to see if it is predicted correctly.
To determine the correlation of flow patterns between Moldflow and the floor, a short shot study was conducted.
The Moldflow process was loaded into the injection molding machine to see if the floor could replicate the Moldflow process.
NOTE: The part data in Moldflow did not include the shelf where the hot drop was located on the part.
The images below show how the short shots on the left very closely match the predicted flow pattern on the right.
Actual short shot vs. Analytical short shot
Actual short shot progression vs. Analytical short shot progression
The pictures below indicate the analysis is predicting flow patterns accurately. However, in both cases (floor and analysis) the part is filling in an imbalanced fashion (the bottom of the part is filling before the top).
Actual short shot near end of fill
Analytical short shot near end of fill
Having confirmed the processes and the filling patterns match, we will now consider the measured deflection.
This image shows the actual measured deflection of the Console, via scan:
The green image below shows the analytical results utilizing the surrogate material overlaid with the scanned floor data, in blue.
Moldflow is predicting the correct downward trend on the top of the part with a 6.49mm variation (underprediction) from the scanned in part. For the sides of the part, Moldflow is also predicting the correct outboard trend with a 6.26mm variation (underprediction). On the bottom of the part, Moldflow is correctly predicting the trend and the magnitude of deflection with a 0.0mm variation.
Overlay analytical part deflection vs. Scanned part deflection
(Actual material)
Noticing that the deflection prediction does not match the floor, we must consider all potential variables. Some of those variables are the available technologies in the software, Midplane, Dual Domain, 3D, BEM Cooling, FEM Cooling, the list goes on. This is where it is important to have a user who has an extensive and enduring understanding of the software in addition to having a good relationship with the software company. This unique collaboration of experienced FEA software experts yields a clear understanding of which technology will work best for the part design.
As part of our due diligence, we also tested each technology in the software and found that the 3D with BEM Cooling had the closest prediction.
For this example, the 3D with BEM Cooling technology was used.
Digging Deeper
Now that we checked all the inputs along with the process, we need to take an even closer look and dig deeper into some of the data that we have less control over, such as the material data.
The material data is a Moldflow .udb file supplied by the material supplier. Upon inspection, all the data fields are populated and none of the data is surrogate.
However, the quality indicators were not populated which raised a flag.
To explain, whenever a material data file is created by a certified Autodesk provider, the quality fields will be populated. Noticing they are not populated raises suspicion about the quality of the remaining data in this material card.
We now had to determine if this material card was valid. To make this determination, we ran the comparison analysis utilizing a material card that we knew was trustworthy and would provide accurate results. We selected a comparable material based on the rheology, thermal and mechanical properties. We utilized the same process settings as previously run with the original material card.
After the comparative analysis was complete, we compared the deflection results with that of the floor. We found that the prediction was not exact, but much more accurate.
The green image below shows the analytical results utilizing the surrogate material overlaid with the scanned floor data, in red. As shown, the predicted results are much closer to reality.
Moldflow is predicting the correct downward trend on the top of the part with a 3.77mm variation (underprediction) from the scanned in part. For the sides of the part, Moldflow is also predicting the correct outboard trend with a 1.88mm variation (underprediction). On the bottom of the part, Moldflow is correctly predicting the trend and the magnitude of deflection with a 0.0mm variation.
Overlay analytical part deflection vs. Scanned part deflection
(Surrogate material)
The analysis with the surrogate material provides results which are closer to that of what is being seen on the floor, about twice (or greater) as accurate as the original material card. Since the material is not the exact grade, we cannot expect it to match up perfectly. However, we now see the influence of the data within the material card on the accuracy of the predictions. If the material data card had correct and trustworthy data, we would be very confident that the results would be almost identical to those on the floor.
In summary, we have looked at a part that was injection molded, scanned for deflection, and compared it to that of the analyzed part. We found that when all process conditions were matched, the predictive deflection results were much greater than that of the actual part.
After a thorough investigation it was found that the material data input (material card) was in question. A quick test was performed with the same analysis utilizing a trustworthy material card which proved to be a more accurate prediction.
It is critical to ensure that all inputs of an analysis are vetted so the precision level of the results are as high as possible. A competent and skilled FEA professional will be able to identify and address any technical issues that may arise to ensure your project results reflect the highest degree of accuracy.