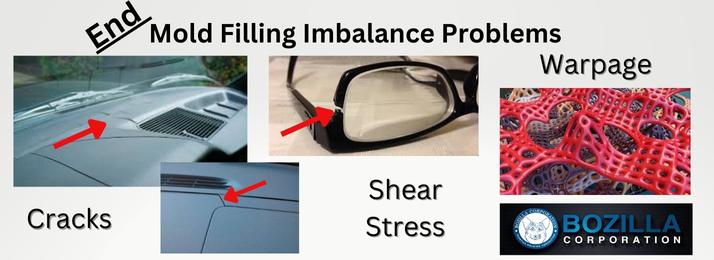
Is Part quality and performance of your injection molded part important? Do you enjoy spending that extra time and money having your tool reworked? How about the pleasure of explaining the faulty part to your OEM? Let’s get real. Balance your tool analytically before mold steel is cut-NO EXCEPTIONS! If you ignore this step, there is a decent chance of experiencing an unfavorable result on complex or seemingly simple tools.
Let’s discuss mold balance.
When can a mold-filling imbalance occur? These imbalances may be due to gate location(s) on the part, part geometry, or a combination of both. Unless it is analyzed in flow simulation software, it is extremely challenging to determine how a part will fill.
What creates an imbalance?
In a single cavity tool, an imbalance can occur when one location of the cavity finishes filling while another has yet to fill.
In a multi-cavity tool and family tool, the same imbalance may occur within each cavity, but an imbalance may also arise from cavity to cavity.
How can imbalances cause problems with part quality and performance?
It is crucial to understand polymer flow. A plastic engineer excels at possessing polymer knowledge. Applying this expertise during the virtual optimization stage of your injection molded part will provide significant insight into an imbalance, which can affect part quality and performance.
Where can an imbalance occur?
As the cavity fills, the temperature of the polymer flowing through the tool must not fluctuate to keep the properties of the polymer consistent throughout the cavity. If flow velocity isn’t uniform in any region of the cavity, hesitation can occur and cause the polymer to cool down. As the polymer cools, a frozen layer will form on the mold walls. This frozen layer forms more rapidly in slower-moving regions and exceptionally fast in areas where the flow has stopped. Once the cavity produces enough pressure to continue filling these hesitating regions, the flow will begin to move again. However, the polymer is now cooler and will create tremendous shear stress as it continues to fill the remainder of the cavity. THIS SHEAR STRESS WILL CREATE THE POTENTIAL FOR PART DEFLECTION AND EVEN PART FAILURE.
If imbalances occur in a multi or family tool, the entire cavity experiencing the hesitation is at risk for this increased shear stress. The imbalance also causes the hesitating region of the cavity to become non-uniformly packed, which translates into non-uniform shrinkage, another precursor to part warpage.
How does shear stress cause quality and performance issues?
When polymer experiences shear stress, the naturally ‘coiled’ molecules are stretched out and frozen into the ‘stretched out’ position within laminates (layers) of the part depending on when and how fast it cools. This process of coiling and uncoiling is called frozen-in stress. Sometimes the stress is so great that the forces can break the molecules.
Frozen-in stresses in a part occur when the molecules are stretched out or broken, and the material cools and solidifies with those molecules in place. Therefore the part now contains a frozen-in level of stress. If these regions of the part have outside forces applied to them, it takes little effort for the part to fail. For example, have you ever purchased a 5-gallon bucket at a home improvement store and had the bottom crack after minimal use? Bye-bye, $10. This story represents a real-life example of how frozen-in stress can cause failure in the field. High-stress regions are usually the first to fail when additional loads are applied in the field as the part functions.
Over time, the stressed molecules can naturally relax into their naturally coiled position. Stress will lessen, and thermal cycling can accelerate this process. For example, the same bucket you purchased has yet to be used and is left outside. It will experience daily thermal cycles allowing the molecules to move and relax, resulting in a wrinkly, warped bottom. Therefore, both time and thermal cycling can relieve the frozen-in stress of a part, causing cracking and/or warpage. e.g., many headaches for you.
Shear stress is invisible
Most of the time, there will be no apparent signs of shear stress or other problems. Shear stress is typically invisible unless the part is so severely stressed that it cracks at the time of molding. Have you examined a clear plastic part, e.g., a CD case, and noticed a rainbow pattern? That is shear stress.
Eliminate shear stress
One of the best ways to prevent shear stress is to avoid an imbalance in the tool. Imbalance in a cavity or a multi (or family) tool can be prevented by performing a mold-filling analysis beforehand. An analysis will provide more insight into the process and the final product so that neither time nor money is lost when creating the tool for any part.
In conclusion, an imbalance in a cavity or a tool can cause molded-in stress, resulting in warpage/deflection or part failure in the field. Are you willing to risk not running an analysis upfront for that expensive mold and having a whole load of problems with your OEM when the parts fail in the field? Do yourself and your company a favor; perform a mold-filling analysis now. You can thank me later. The Bozilla corporation team saves their customers’ jobs and reputations, one part at a time.
Contact Bozilla Corporation today and let’s discuss how we can successfully contribute to your project. Bozilla Corporation’s Injection molding Team has over 20 years of experience analytically and on the floor. We specialize in optimization, consulting, engineering, troubleshooting and Autodesk Moldflow software custom training and mentoring. Additionally, our plastics engineers have a full understanding of polymers and how they influence an injection molded part. Your success is our success. Our skilled Team is focused upon meeting the goals and timelines of our customers.
www.BozillaCorp.com, 800-942-0742, info@BozillaCorp.com
About Bozilla Corporation: https://youtu.be/HIUfzwf1x90
About the Author:
Chris Czeczuga is a Plastics Engineer, Injection molding expert, Military Veteran and the President of Bozilla Corporation. He has proven success with many Fortune 500 companies throughout the injection molding industry. A graduate from UMass Lowell, he is Expert Certified with Autodesk, has 20+ years of field experience, intimate knowledge of injection molding part, tool and feed system design. Bozilla Corporation’s success is built on providing the highest level of injection molding simulation and consulting advice to businesses who have short lead times, require an efficient, cost-effective molding process, and desire to produce a correct part the first time.