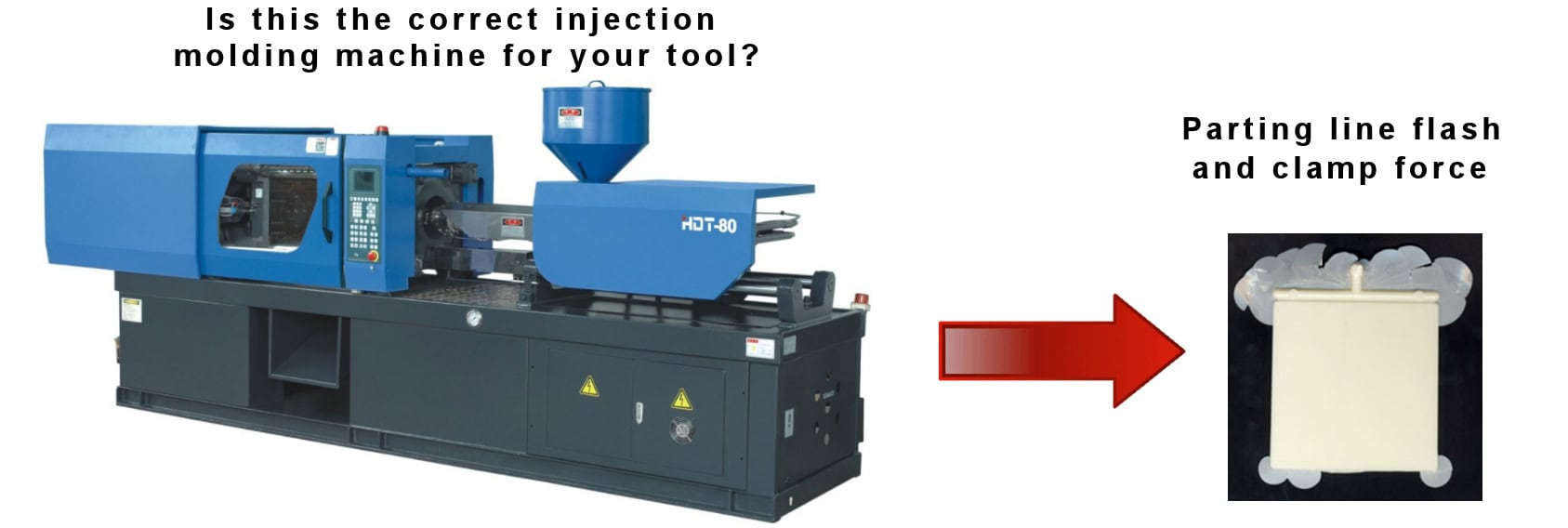
To start this discussion I’d have to first state that the size of the tool plays a large role when selecting an injection molding machine. More specifically, it is the projected area that is of concern and how the projected area, along with the pressure distribution over that projected area, creates clamp force.
Selecting a machine based on clamp force (tonnage) is more common when you have a part with a large projected area; i.e. multi-cavity tools, bumper fascias, housewares and many other items.
In today’s economic climate, it’s more important than ever to conserve energy. Many believe that using the smallest IMM is the best way to achieve this cost savings. However, there are reasons why a smaller machine isn’t always the most efficient machine.
Reason 1: If an optimum process is the objective, select a machine that does not allow the tool to exceed the clamp force and flash the tool (blowing open) during an ‘optimized’ process.
We have had many concerned customers consult with us about the process. Their questions are directed at finding out why the part is warping or exhibiting cosmetic defects. Once I dig into the process, I typically find that the part is not packed sufficiently due to the tool blowing open. In order to keep the tool closed, they must pack with very little pressure for a very short time. Packing with too little pressure, too little time, or both can cause a loss of control with dimensional stability and/or cosmetic issues due to excessive shrinkage. These issues create problems that are caused because the tool is in an IMM that doesn’t have the proper clamp force requirement.
In the image below the clamp force required to fill and make the part is 250 Tons. However, in order to pack the part out sufficiently and make a good part (meets tolerances, minimal cosmetic defects, minimal deflection, etc.) the clamp force required during 2nd stage pack is 1,450 Tons. That’s a very big difference.
Reason 2: You are able to make parts but the process window is so small that staying within the process window is difficult or impossible to maintain.
The inability to stay within a process window could be caused by several issues, especially since there are so many variables in the molding process. However, if the machine does not have sufficient clamp force to stay closed during an optimum molding process, concessions will be made and you may find yourself on the edge or on the outside of the molding window. For example, in order to keep the clamp closed, the process may need to be pressure limited. Limiting the pressure can prevent the part from being filled and/or packed sufficiently. Once this happens, its very difficult to find a molding window for the duration of production for that tool. Utilizing a process that does not have a proper molding window proves inefficient with regards to waste, lost productivity, lost man hours, excessive energy consumption, etc.
Reason 3: Valve gates (if applicable) are closed prematurely during 2nd stage to prevent the clamp from blowing open.
Here is a common practice that often ends in poor part production. Valve gates are not as simple as many often think. When valve gates are sequenced, the 1st stage injection velocity must be profiled to accommodate the extra valve gates opening. Similarly, during 2nd stage, the valve gates must remain open until the part freezes up to the gate (very near the gate but not on the gate). If any valve gate is closed before the part freezes, the chances of having backflow increases dramatically. Backflow is a condition where material either changes direction or stops then starts again. Both backflow situations can cause tremendous stress and could produce a fracture between laminae within the part. Furthermore, the part will not be packed in the region of the valve gate that has been closed. The underpacked region will shrink excessively potentially losing mold surface texture, rippling, sink or a host of other cosmetic issues. A part that is not packed sufficiently is susceptible to high volumetric shrinkage which is a precursor to warpage.
Reason 4: The reject rate is high leading to lost revenue
A high reject rate may be due to the inability to stay within the optimum molding window resulting in a ‘floating’ process that changes because of any slight variation. The inability to stay within a molding window may be due to the clamp force controlling the process rather than the process settings controlling the process. High injection rates costs valuable time, money and resources.
In conclusion, it is more crucial than ever to specify an injection molding machine (IMM) worthy of the process required for that part, especially parts with a large projected area. This is not a simple hand calculation based on the type of resin used (X Tons of clamp force per square inch based on a specific type of resin). It becomes more complicated than that and is typically a function of the pressure distribution over the projected area during 2nd stage pack.
So how do you know what the required clamp force will be for your part? A flow analysis will provide the answer.
The Team at Bozilla Corporation are plastics engineers with over 20+ years of analytical and floor experience. We can perform a flow analysis and consult with you to ensure you are making the best choice for selecting an appropriate sized Injection Molding Machine for your project. Contact us today and let’s get started!
www.BozillaCorp.com– Injection Molding Specialists- engineering, consulting, optimization, failure diagnosis, training
About the Author
Chris Czeczuga is a Plastics Engineer, Injection molding expert, Military Veteran and the President of Bozilla Corporation. He has proven success with many OEM’s, Tier 1’s, Tier 2’s, Tool Shops, Molding Shops, Part Designers, Processors and Fortune 500 companies throughout the injection molding industry. A graduate from UMass Lowell, he is Expert Certified with Autodesk, has 20+ years of field experience, intimate knowledge of injection molding part, tool and feed system design. Bozilla Corporation’s success is built on providing the highest level of injection molding simulation and consulting advice to businesses who have short lead times, require an efficient, cost-effective molding process, and desire to produce a correct part before mold steel is cut.