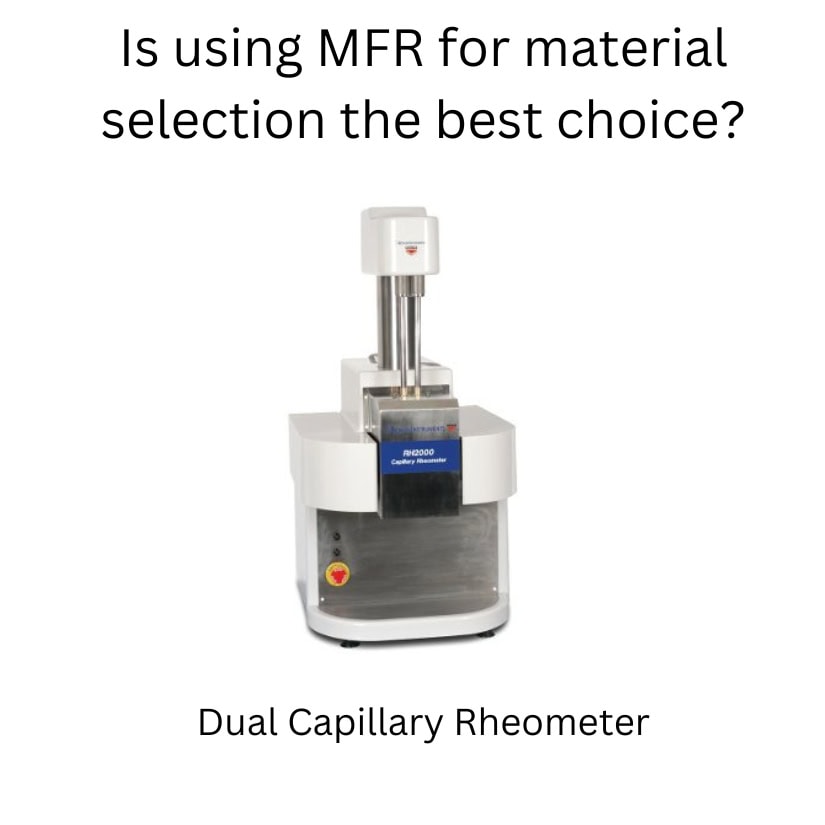
When a material selection comes down to flow rate, is using the (Mass Flow Rate) MFR or Melt Index (MI) the best choice? To answer this, we need to understand why the Melt Index test initially came about.
The Origin of the Melt Index Test Method (ASTM D-1238)
ASTM D 1238: Test Method for Flow Rates of Thermoplastics by Extrusion Plastometer.
Before there were standards to test polymers, there was a need to determine the differences in how polymers would flow when melted. A method was created to keep all polymers on the same level playing field. This method places the material in an Extrusion Plastometer or Melt Indexer.
The standard has the barrel of the melt indexer heated to a specific temperature. The user would obtain a resin sample and place it in the barrel where a piston would be inserted. A specific load would be placed on the piston, and the melted polymer would be extruded through a capillary die (with a particular orifice size). The extrusion would take place for 10 minutes, and the amount of polymer would be weighed in grams yielding an output in g/10 minutes.
Having MFR data for all materials allows one to compare them side-by-side, giving a respective idea of how each will flow with the other.
The limitation of this test method is that it is, in fact, one point on the viscosity curve and is at a shear rate of nearly zero, which is not indicative of the injection molding process.
When materials experience shear during injection molding, shear rates may be experienced up to and possibly exceeding 100,000 1/sec. Some materials become more viscous at higher shear rates, but these are uncommon.
So how do we compare materials at these higher shear rates?
Since the inception of the melt indexer (1950s), a much more accurate test method was designed using a Dual Capillary Rheometer.
A dual capillary rheometer can produce a series of viscosity data points over a range of shear rates, such as the image below.
A Rheology curve provides exact viscosity data based on specific shear rates at specifically tested temperatures. Notice how the Melt Index MFR point does not provide any data relating to the injection molding process. A curve like this will allow one to understand the exact behavior of the material and shear rate at the processing temperature used during molding. When two materials are compared, this curve will tell them if one material will flow more readily.
Currently, most testing takes place on an injection molding machine fitted with a unique die head that has a rectangular slit and is instrumented accordingly to acquire all of the necessary data for broad-spectrum rheology testing. The benefits of testing on an injection molding machine include the consideration of melt homogeneity and material degradation. Utilizing an injection molding machine for rheology testing is the best and most comprehensive method used today.
In conclusion, the ASTM D1238 Melt Index Test Method (MFR) is a great way to compare one material to another using zero shear flow rates. However, the reality is that when materials are injection molded, the shear rates are far from zero. At higher shear rates, it’s imperative to understand flow behavior of a polymer. The only way to do this is to look at and compare the rheology curve produced by the dual capillary rheometer or, better yet, a properly outfitted injection molding machine.
Bozilla Corporation utilizes completely tested rheology curves for every project to gain a thorough understanding of the polymer chosen for the application. Using this data provides the most remarkable accuracy when analyzing projects within the Autodesk Moldflow software when investigating polymers for project application and project troubleshooting.
Contact Bozilla Corporation today and let’s discuss how we can successfully contribute to your project. Bozilla Corporation’s Injection molding Team has over 20 years of experience analytically and on the floor. We specialize in optimization, consulting, engineering, troubleshooting and Autodesk Moldflow software training. Additionally, our plastics engineers have a full understanding of polymers and how they influence an injection molded part. Your success is our success. Our skilled Team is focused upon meeting the goals and timelines of our customers.
www.BozillaCorp.com, 800-942-0742, info@BozillaCorp.com
About Bozilla Corporation: https://youtu.be/HIUfzwf1x90
About the Author:
Chris Czeczuga is a Plastics Engineer, Injection molding expert, Military Veteran and the President of Bozilla Corporation. He has proven success with many Fortune 500 companies throughout the injection molding industry. A graduate from UMass Lowell, he is Expert Certified with Autodesk, has 20+ years of field experience, intimate knowledge of injection molding part, tool and feed system design. Bozilla Corporation’s success is built on providing the highest level of injection molding simulation and consulting advice to businesses who have short lead times, require an efficient, cost-effective molding process, and desire to produce a correct part the first time.