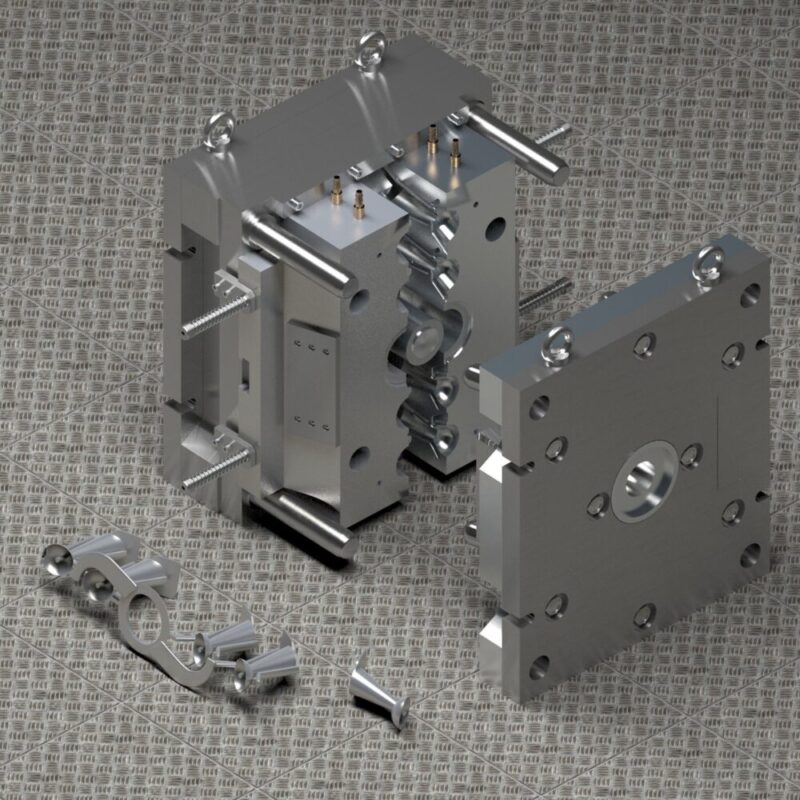
Aluminum tooling has significant benefits when compared to steel tooling because of the cost of aluminum as well as the ease of manufacturing. Aluminum tools can be cut much quicker than steel saving a lot of time and money. These benefits can result in shorter cycle times and price-per-part savings. However, there are some drawbacks of aluminum such as being a softer metal which can cause mold deflection and also having a fatigue limit which can be catastrophic. In order to better understand the advantages and disadvantages of utilizing aluminum for injection molds we will take a closer look at the properties of both aluminum and steel.
Let’s compare the properties of aluminum to steel.
Table of Aluminum v. Steel properties
The above table compares the properties of aluminum and steel. Based on this table, we can determine the following.
Density: Aluminum is 2.79 times less dense than Steel
Hardness: Aluminum is much softer than steel.
Thermal Conductivity: Aluminum is 6.55 times more conductive than Steel
Thermal Diffusivity: Aluminum has 7.9 times the thermal diffusivity than Steel
Yield Strength: Aluminum has almost half of the yield strength of Steel
Poissons Ratio: Aluminum deforms more than Steel
Advantages of Using Aluminum for Injection Molds
Now that we’ve compared aluminum to steel, we can take a look at the advantages of using aluminum for injection molds based on the above properties.
Density:
Aluminum is 2.79 times less dense than steel resulting in a lighter end product. As the cost of shipping is increasing dramatically, the weight of any product will have a direct impact on shipping costs and must be kept low as possible
Hardness:
The softer aluminum reduces machining hours and wear and tear on machining components
Thermal Conductivity and Diffusivity:
Thermal conductivity and diffusivity is extremely important in injection molding as it directly impacts the cycle time. Aluminum is 6.55 times more conductive and 7.99 times the diffusivity of steel which results in a significant reduction in cycle time, faster start-up times, reduction in response times to process temperature changes, and mold change times.
The faster thermal recovery of aluminum also modulates the cyclic ‘highs-and lows’ of the tool temperature during processing. As the melt is injected into the mold, the heat must be removed as quickly as possible. Aluminum is able to process the heat out of the tool much faster than steel resulting in a more stable mold temperature and thus a more stable process.
Disadvantages of Using Aluminum for Injection Molds
Poissons Ratio:
The Poissons Ratio of Aluminum is 0.33 and Steel is 0.29 which simply put: Aluminum is more elastic than Steel. Higher elasticity can translate into issues as aluminum has a fatigue limit where steel does not.
The image above illustrates the difference in fatigue limits of steel versus aluminum. The fatigue of steel (stress) reduces slightly during the early cycling phase and then levels off and is able to continue cycling without the onset of further fatigue. However, when looking at the fatigue of aluminum (stress), it continues to decrease as cycling continues which ultimately leads to failure.
Yield Strength:
The yield strength of aluminum is nearly half that of steel which could result in failure of the mold should the pressure and stresses within the mold get too high..
If the tool has any individual core components which can deform, we have to consider how much they will deform and how many cycles the tool will experience before the cores will ultimately fail. An aluminum tool that has any deformation will have a finite life span.
Even if there are no individual core components to deflect within the tool, the tool itself can deflect as seen below.
If there is high cavity pressure, then the aluminum tool will want to deflect much more than a steel tool. If this kind of deflection occurs, then the machine platens will have to take on the burden of the tool flexing which can put excessive wear and tear on a machine. It might even be necessary to create a steel frame enclosure for the aluminum tool to ensure deformation does not get translated to the machine platens. In some cases, the machines platens must be thicker to accommodate the tool deflection.
In summary, with regards to injection molds, aluminum has significant benefits when compared to steel.
Advantages:
- Lower Density = Lower shipping costs
- Lower Hardness = Faster milling time, less wear and tear, reduced time to manufacture.
- Thermal properties = More stable process, faster start-ups, faster process response times and faster cooling/cycle times.
Disadvantages:
- More elastic = mold deformation, mold core deformation and Injection Molding Machine wear
- Fatigue limit = A lifespan on the mold and internal components i.e. Potential for mold cores and even mold failure
Understanding the benefits and disadvantages and weighing them both carefully will provide the knowledge and insight of when to utilize the aluminum tool over the steel tool. Without this knowledge the decision can potentially lead to higher over-all costs and even the catastrophic failure of the tool.
If core deflection is a concern, Bozilla Corporation can run an analysis and identify any core deflection and the magnitude of that deflection via simulation analysis.
For more information, support with your Tool Design, assistance Troubleshooting any of your Plastics Injection Molded projects, or Autodesk Moldflow Training contact the Team at Bozilla Corporation.
Bozilla Corporation’s Plastics Injection Molding Team has over 20 years of experience analytically and on the floor. We specialize in optimization, consulting, engineering, troubleshooting and Autodesk Moldflow software training. Additionally, our plastics engineers have a full understanding of polymers and how they influence an injection molded part. Your success is our success. Our skilled Team is focused upon meeting the goals and timelines of our customers.
www.BozillaCorp.com, 800-942-0742, info@BozillaCorp.com
About Bozilla Corporation: https://youtu.be/HIUfzwf1x90