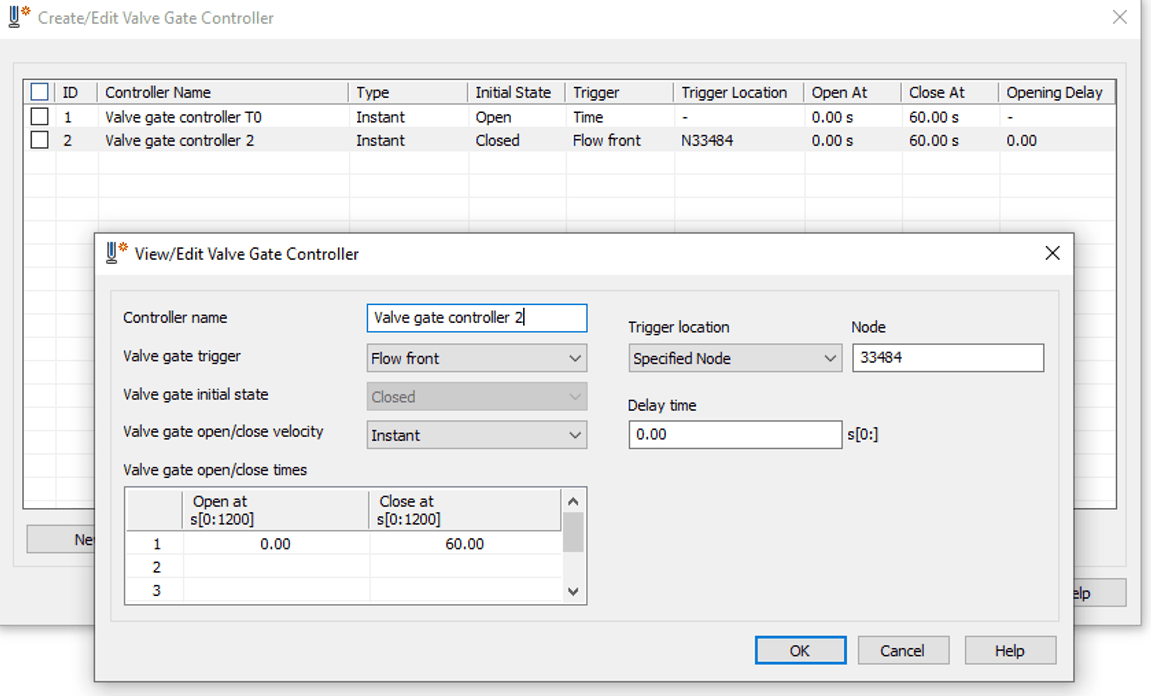
Valve Gates are invaluable as they relate to their primary design purpose and have many important functions.
They can:
✔ Eliminate waste that cold runners create
✔ Eliminate vestige
✔ Be sequenced
✔ Eliminate weld lines
✔ Control filling patterns
However, users should be aware that there are a few potential issues that could come with using valve gates and sequencing.
Vestige v. Witness Marks
Valve gates can minimize or completely remove vestige by direct gating on the part. They do leave witness marks on the part where the valve gate tip seats into the cavity but with proper grinding or surface finish, it can be minimized or completely hidden.
Controlling the Fill Pattern v. Machine Stroke Programming
When multiple valve gates are used to fill a part, it may be necessary to time the sequencing in order to create a more uniform filling pattern. It is extremely important to understand that if the valve gates are sequenced, then the flow rate input must also match the demand of the feed system.
For example: If your tool has four valve gates and you initially open two valve gates, then open the next two valve gates, the IM machine must deliver twice the flow rate when the two additional valve gates are opened in order to maintain equal flow rates through all nozzles in the feed system.
If the machine stroke is not profiled to compensate for the flow rate demand, the properties of the polymer will change in the cavity due to different filling rates. This could translate into non-uniform shrinkage and stress which directly translates into warpage. It can also cause surface finish variations as shown in the picture below.
Cascade Sequencing (eliminate weld lines) v. Machine Stroke Programming
If the intention is to sequence the valve gates as the flow front passes by in order to remove weld lines, then the same concerns arise if the machine stroke is not programmed to compensate for the additional flow rate demand as additional nozzles are opened.
Cascade sequencing can also create back-flow and uneven packing along with uneven stress even if the machine stroke is profiled to compensate for flow rate.
Cascade sequencing removes weld lines, therefore the potential problems that accompany it must be weighed. Cascade sequencing should be used as a last resort when trying to eliminate weld lines.
Valve Pin Control
Hot runner manufacturers have now developed controllers to move the valve pin at a specified rate. This allows the user to open the valve pin slowly which prevents the sudden burst of polymer into the cavity thus preventing the sudden loss of pressure in the feed system which causes hesitation in other regions of the cavity. This is an extremely useful implementation but does come at a cost and can be tricky to set up.
Conclusion
Even though valve gates can aid in creating parts with little or no vestige, they have other purposes that can help the molding process. These other purposes can come with implications which can instigate problems if not considered.
The use of FEA (Mold filling analyses) can be used to take full advantage of valve gate sequencing. It can also address most, if not all, of the potential issues that can occur from the use of valve gate sequencing. Without the use of such tools, the potential for complication is fairly high. To limit difficulties and setbacks, contact an injection molding professional who will offer solutions and feedback to avoid or correct issues that arise.
About the author
Chris Czeczuga is a Plastics Engineer, Injection molding expert, Military Veteran and the President of Bozilla Corporation. He has proven success with many OEM’s Tier 1’s, Tier 2’s, Tool Shops, Molding shops, Part Designers, Processors and Fortune 500 companies throughout the injection molding industry. A graduate from UMass Lowell, he is Expert Certified with Autodesk, has 20+ years of field experience, intimate knowledge of injection molding part, tool and feed system design. Bozilla Corporation’s success is built on providing the highest level of injection molding simulation and consulting advice to businesses who have short lead times, require an efficient, cost-effective molding process, and desire to produce a correct part before mold steel is cut.