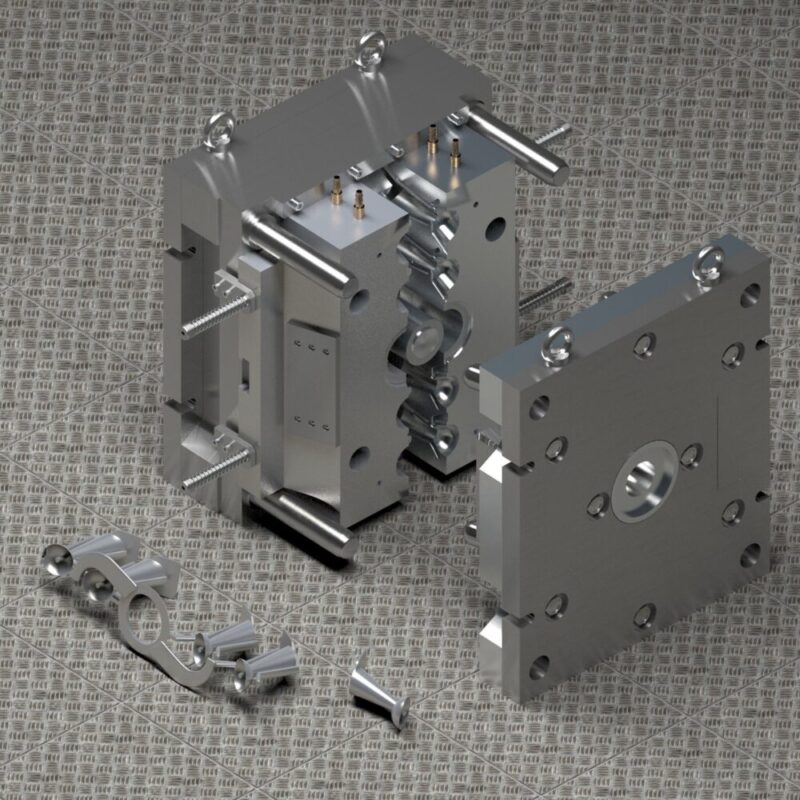
Using Aluminum for Injection Molds?
Aluminum tooling has significant benefits when compared to steel tooling because of the cost of aluminum as well as the ease of manufacturing Aluminum tools can be cut much quicker than steel saving a lot of time and money These benefits can result in shorter cycle times and price-per-part savings However, there are some drawbacks of aluminum such as being a softer metal which can cause mold deflection and also having a fatigue limit which can be catastrophic In order to better understand the advantages and disadvantages of utilizing aluminum for injection molds we will take a closer look at the properties of both aluminum and steel
Let’s compare the properties of aluminum to steel
Table of Aluminum v Steel properties
The above table compares the properties of aluminum and steel Based on this table, we can determine the following
Density: Aluminum is 279 times less dense than Steel
Hardness: Aluminum is much softer than steel
Thermal Conductivity: Aluminum is 655 times more conductive than Steel
Thermal Diffusivity: Aluminum has 79 times the thermal diffusivity than Steel
Yield Strength: Aluminum has almost half of the yield strength of Steel
Poissons Ratio: Aluminum deforms more than Steel
Advantages of Using Aluminum for Injection Molds
Now that we’ve compared aluminum to steel, we can take a look at the advantages of using aluminum for injection molds based on the above properties
Density:
Aluminum is 279 times less dense than steel resulting in a lighter end product As the cost of shipping is increasing dramatically, the weight of any product will have a direct impact on shipping costs and must be kept low as possible
Hardness:
The softer aluminum reduces machining hours and wear and tear on machining components
Thermal Conductivity and Diffusivity:
Thermal conductivity and diffusivity is extremely important in injection molding as it directly impacts the cycle time Aluminum is 655 times more conductive and 799 times the diffusivity of steel which results in a significant reduction in cycle time, faster start-up times, reduction in response times to process temperature changes, and mold change times
The faster thermal recovery of aluminum also modulates the cyclic ‘highs-and lows’ of the tool temperature during processing As the melt is injected into the mold, the heat must be removed as quickly as possible Aluminum is able to process the heat out of the tool much faster than steel resulting in a more stable mold temperature and thus a more stable process
Disadvantages of Using Aluminum for Injection Molds
Poissons Ratio:
The Poissons Ratio of Aluminum is 033 and Steel