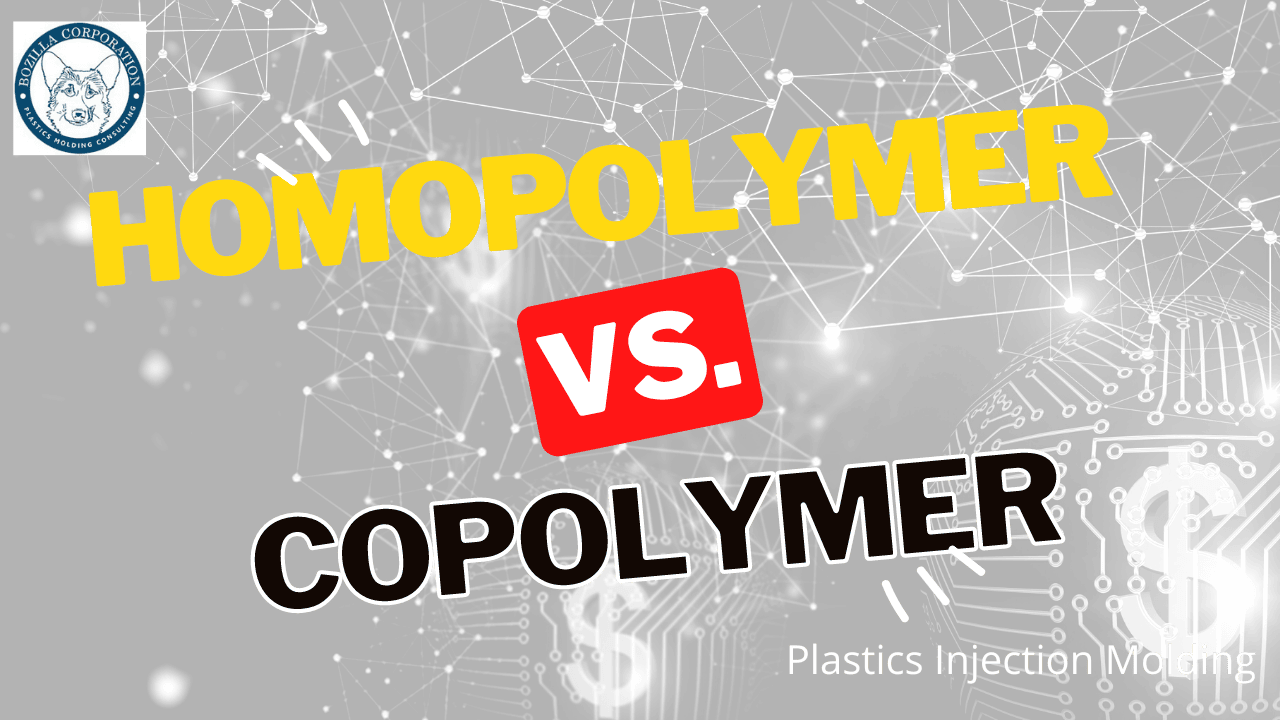
Homopolymer vs. Copolymer
Material selection for an injection molding application can sometimes prove to be very challenging What happens if you identify a material then find that it can be supplied as a homopolymer or a random copolymer Is there a difference? The answer is YES The choice made for your project can affect part quality
The Homopolymer:
A homopolymer has the same base unit which causes the molecular chain to have a high degree of consistency and size However, length can vary depending on how long the polymerization process is allowed to occur
The high degree of consistency in a homopolymer creates a high degree of regularity When many of these changes flow and combine, they are able to create a very tight entanglement and when they cool and shrink, they also have a high degree of crystallinity which increases shrink
The Copolymer:
A copolymer, as shown in the image above, has more than one base unit and each base unit is a different size There can be more than two base units Due to the variation in size of the base units, the copolymer chains will be spaced much further from each other and have a higher degree of irregularity And similar to the homopolymer, the length of the molecule will depend on how long the polymerization process is allowed to occur
The high degree of irregularity does not allow the polymer chains to form a tight structure, leaving a lot of space between the molecular chains Therefore, when the polymer flows, there can be alignment but there will be more irregularity and not as tight of a structure which prevents excessive shrinkage
When comparing the two types of polymers, assuming each is the same length (same molecular weight, per se) the homopolymer will be much more organized and structured therefore creating more mechanical strength and chemical resistance but have high shrinkage The copolymer will have more random orientation which will create space between the molecules allowing for easier chemical attack and less mechanical strength and also have lower shrinkage Of course, we could discuss these comparisons in much more detail but we will stick to the basics for now
As material selection relates to injection molding, the properties of the material is a crucial factor
The major properties when comparing homopolymers to copolymers are:
- shrinkage
- chemical resistance
- mechanical strength
Each of these properties must be considered with regards to the outcome of part quality
For example, when injection molding