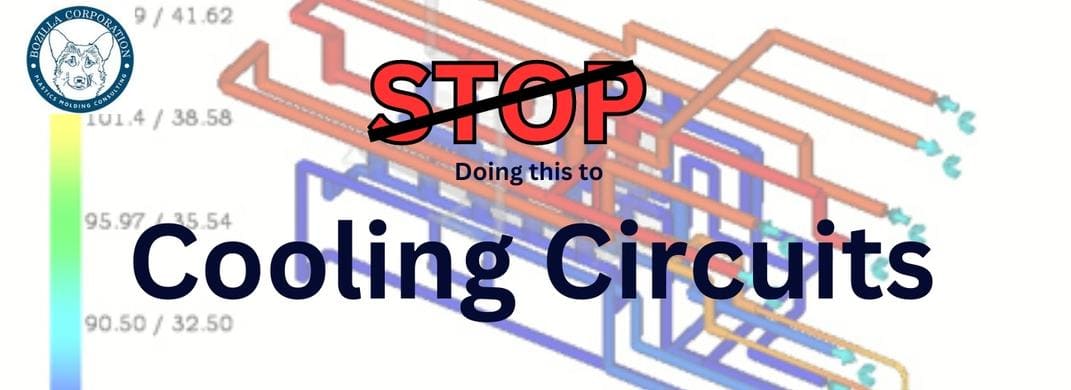
STOP doing this to Cooling Circuits!
STOP ignoring the importance of proper cooling circuit design for injection molding Cooling circuit design is typically not heavily weighted with regards to importance in the injection molding industry Cooling circuits need to be designed properly and the importance of the design must not be overlooked A common practice is to simply ‘place cooling in the mold’ and not much more Sometimes it is taken a step further where the practice is ‘to place as much cooling in the mold as possible’ This is a better practice but is it the best? We are going to discuss the importance of proper cooling circuit design and the implications of overlooking this important practice
Cooling Circuit Diameter
Is the diameter of the cooling circuit important? It certainly is In fact, the diameter of the cooling circuit must be a part of a larger consideration such as circuit spacing, pressure drop and flow rates A larger diameter may be thought to cool better since it is larger, which is somewhat true, however it will take up more space due to its larger diameter so it may be difficult to route in tighter locations
The spacing of larger cooling lines can be increased based on the diameter which can result in fewer cooling lines hence less gun—drilling, ie a cost savings but this is not always the better condition if the mold design is complex or small Larger cooling lines will also have a lower pressure loss resulting in less power required to pump the water through the circuit This is a big plus but the difference in pumping efficiency may be negligible It is also important to understand that varying cooling circuit diameters within the same mold will only be as efficient as the smallest diameter of that circuit due to the higher pressure loss within the section containing the smaller diameter The flow may be turbulent in the portion with the smaller diameter yet may take flow away from the larger diameter portion resulting in a laminar flow condition in the section with that larger diameter
The Importance of Balanced Cooling Circuits
Optimal designed cooling circuits are the driving force behind productivity and cycle times
If your cooling circuits are not as working as efficiently as they can be, they will be costing you precious time and money Balancing cooling circuits plays a tremendous role in cooling efficiency
So why do the cooling circuits need to be balanced and what exactly does that mean?
In short, all circuits are not created equal If cooling circuits are not equally balanced, then the flow rate