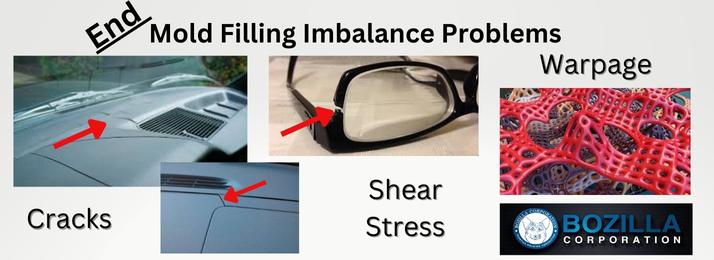
End Part Failure due to Mold Filling Imbalance
Is Part quality and performance of your injection molded part important? Do you enjoy spending that extra time and money having your tool reworked? How about the pleasure of explaining the faulty part to your OEM? Let’s get real Balance your tool analytically before mold steel is cut-NO EXCEPTIONS! If you ignore this step, there is a decent chance of experiencing an unfavorable result on complex or seemingly simple tools
Let’s discuss mold balance
When can a mold-filling imbalance occur? These imbalances may be due to gate location(s) on the part, part geometry, or a combination of both Unless it is analyzed in flow simulation software, it is extremely challenging to determine how a part will fill
What creates an imbalance?
In a single cavity tool, an imbalance can occur when one location of the cavity finishes filling while another has yet to fill
In a multi-cavity tool and family tool, the same imbalance may occur within each cavity, but an imbalance may also arise from cavity to cavity
How can imbalances cause problems with part quality and performance?
It is crucial to understand polymer flow A plastic engineer excels at possessing polymer knowledge Applying this expertise during the virtual optimization stage of your injection molded part will provide significant insight into an imbalance, which can affect part quality and performance
Where can an imbalance occur?
As the cavity fills, the temperature of the polymer flowing through the tool must not fluctuate to keep the properties of the polymer consistent throughout the cavity If flow velocity isn’t uniform in any region of the cavity, hesitation can occur and cause the polymer to cool down As the polymer cools, a frozen layer will form on the mold walls This frozen layer forms more rapidly in slower-moving regions and exceptionally fast in areas where the flow has stopped Once the cavity produces enough pressure to continue filling these hesitating regions, the flow will begin to move again However, the polymer is now cooler and will create tremendous shear stress as it continues to fill the remainder of the cavity THIS SHEAR STRESS WILL CREATE THE POTENTIAL FOR PART DEFLECTION AND EVEN PART FAILURE
If imbalances occur in a multi or family tool, the entire cavity experiencing the hesitation is at risk for this increased shear stress The imbalance also causes the hesitating region of the cavity to become non-uniformly packed, which translates into non-uniform shrinkage, another precursor to part warpage
How does