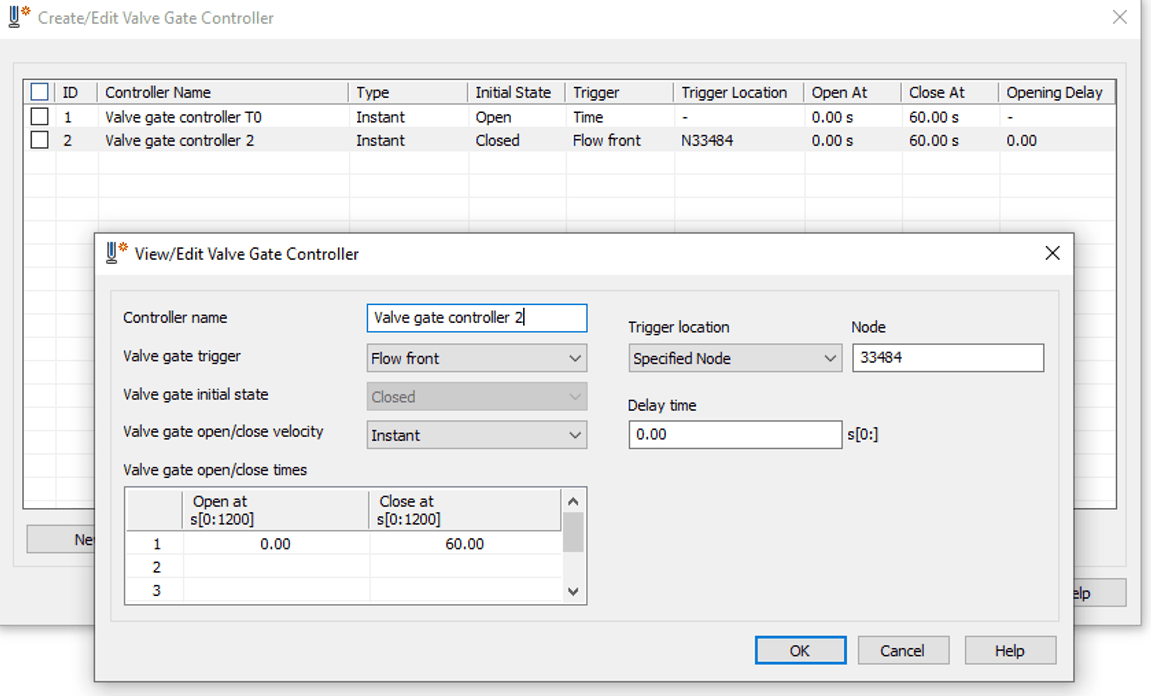
Valve Gates and Sequencing-for injection molding
Valve Gates are invaluable as they relate to their primary design purpose and have many important functions
They can:
✔ Eliminate waste that cold runners create
✔ Eliminate vestige
✔ Be sequenced
✔ Eliminate weld lines
✔ Control filling patterns
However, users should be aware that there are a few potential issues that could come with using valve gates and sequencing
Vestige v Witness Marks
Valve gates can minimize or completely remove vestige by direct gating on the part They do leave witness marks on the part where the valve gate tip seats into the cavity but with proper grinding or surface finish, it can be minimized or completely hidden
Controlling the Fill Pattern v Machine Stroke Programming
When multiple valve gates are used to fill a part, it may be necessary to time the sequencing in order to create a more uniform filling pattern It is extremely important to understand that if the valve gates are sequenced, then the flow rate input must also match the demand of the feed system
For example: If your tool has four valve gates and you initially open two valve gates, then open the next two valve gates, the IM machine must deliver twice the flow rate when the two additional valve gates are opened in order to maintain equal flow rates through all nozzles in the feed system
If the machine stroke is not profiled to compensate for the flow rate demand, the properties of the polymer will change in the cavity due to different filling rates This could translate into non-uniform shrinkage and stress which directly translates into warpage It can also cause surface finish variations as shown in the picture below
Cascade Sequencing (eliminate weld lines) v Machine Stroke Programming
If the intention is to sequence the valve gates as the flow front passes by in order to remove weld lines, then the same concerns arise if the machine stroke is not programmed to compensate for the additional flow rate demand as additional nozzles are opened
Cascade sequencing can also create back-flow and uneven packing along with uneven stress even if the machine stroke is profiled to compensate for flow rate
Cascade sequencing removes weld lines, therefore the potential problems that accompany it must be weighed Cascade sequencing should be used as a last resort when trying to eliminate weld lines
Valve Pin Control
Hot runner manufacturers have now developed controllers to