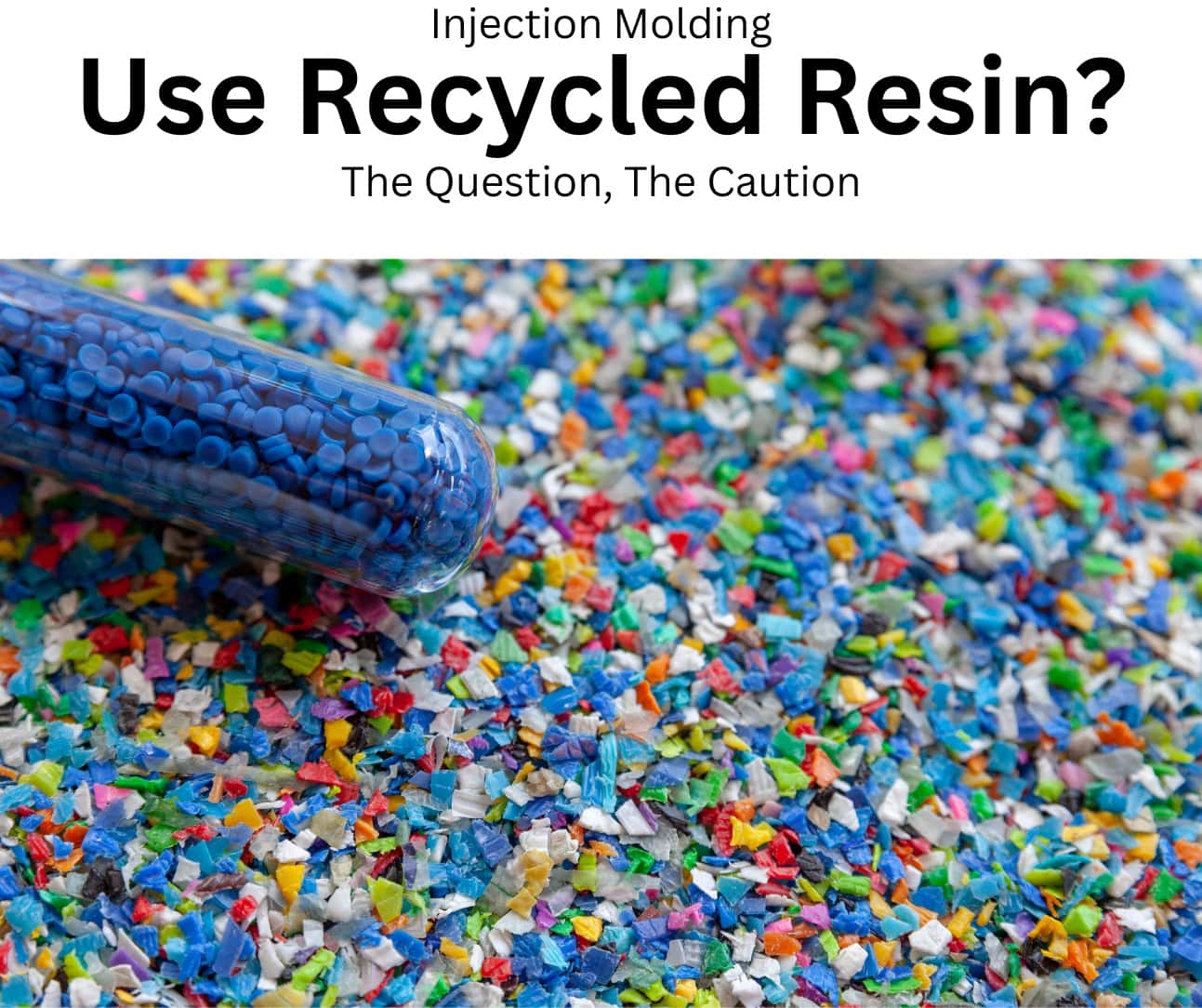
Recycled Resin- The Question and the Caution
By: Bozilla Corporation
My customer doesn’t like using any recycled material
Working with a Tier 1 supplier to a major OEM, there was a discussion with the molders on the floor, people molding the parts on the injection molding machine, and their personal experiences
Their experience with recycled resins is the inability to maintain a controlled injection molding process
Because they are responsible for the quality of the part they are molding, they make decisions (call an audible) and replace the recycled resin with a locally available equivalent virgin resin This protects them from producing unacceptable
Losing Control of the Process
Recycled plastic goes through several processes when it is reclaimed In layman’s terms, it gets beaten up
Here is the rundown:
In the first phase of the plastic recycling process, the material goes through the injection molding process, which partially degrades the material (molecular weight reduction) Then, it is potentially exposed to UV, temperature fluctuations, or chemicals, which contributes to the degradation process Next, the plastic is ground up and typically cleaned with a thermal or chemical process, further degrading the material Finally, the reclaimed plastic is ready to, again, be beaten up in the injection molding machine
Loss of injection molding process control
It is essential to know that the reclamation process breaks the polymer’s molecular structure down, making it lesser quality because the properties of that original polymer have been degraded Recycled resin has a smaller molecular weight( length of chains) and varying viscosity, making it unpredictable Virgin resin has molecular weight consistency/control with much less variation, giving it consistent properties
This lack of consistency, or better stated, lack of control of the recycled resin will affect the quality of your part
Do you see some reasons why you may reconsider using recycled plastic for your part?
Industry Response
Now, the response in the industry and all industries to using recycled materials is, when possible, to take a certain percentage of recycled material and blend it in with the virgin resin
However, it is essential to note that the percentage of added recycled material vs part quality is not a 1:1 ratio, eg, adding 20% of recycled resin does not equate to 20% loss of properties For instance, you can test the recycled resin of 1 lot of material, and it may meet specs, but the next lot is completely different, thus knocking the process out of control This lack of conformity